Going paperless drives operational efficiencies and cost savings
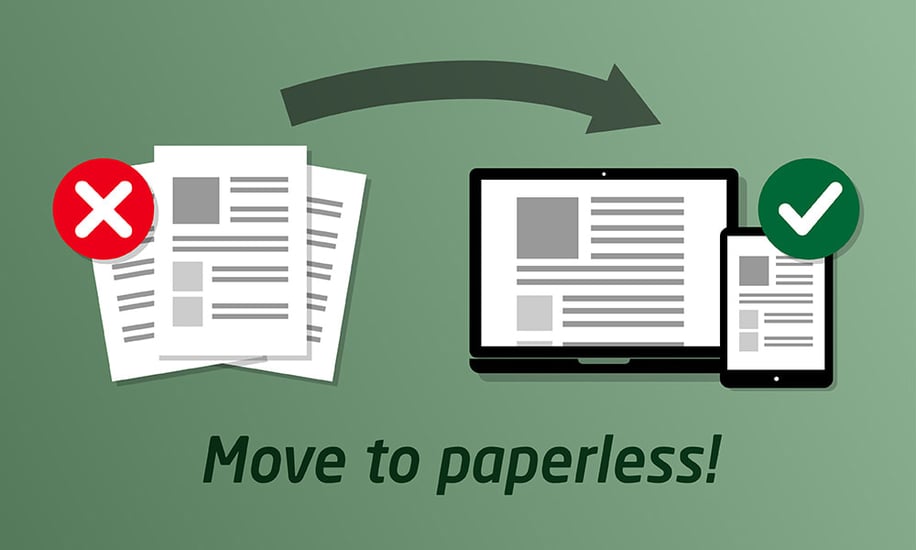
Hills Waste Solutions embraces technology enthusiastically in a number of ways across the business, from route planning and GPS tracking for our collection vehicles, through to online portal access which provides useful reporting tools and waste management documentation for our customers.
Not to rest on our laurels, our Area Depot Manager, Neil Luce, had a vision to reduce, or completely remove the need for paper within our operational depots, which help run our fleet of trucks for collecting customer waste. With this vision came the benefit of reducing our impact on the environment, helping to avoid unnecessary waste, though this was not the main goal of the project.
In starting this initiative, Neil recognised that we had an opportunity to make improvements in certain areas of our operational processes:
- Daily Vehicle Check sheets and work schedules containing each site to be visited, were typically produced, 6 sheets of paper for each truck, each day, consuming valuable energy when printing them out, using lots of paper, printer ink, ink cartridges, and administrative time in keeping the photocopiers operating.
- Sometimes, with early completion of a round, drivers would return to the office to pick up additional Waste Transfer Notes before they continued on their rounds. This was time consuming and inefficient, using up valuable fuel.
- Wear and tear and any damage to vehicles would not be reported until the end of the day, delaying repairs, possibly leading to longer vehicle down time.
- Small screens with existing tablets made them more difficult to use in cab.
- A frustrating, but important, feature of ink is that it fades with time, which is a problem for a regulated industry where it may be necessary to refer to documents many years later.
So finding a digital solution to overcome these issues was very desirable.
To deliver the project, it was necessary to update the in-cab technology for our drivers to provide them with the latest tablets which would allow direct connectivity to and from the depots. Importantly however this upgrade provided the means to give our drivers much more functionality.
Pre-start checksThe new tablets help our drivers to do their pre-start checks digitally, rather than on paper. This also allows the drivers to take pictures of the vehicle to evidence that it is in good working order before starting out, and, at the end of the shift, to evidence that the vehicle is still in good working order. This helps to protect the driver from being responsible for damage that may have occurred before he takes over control of the vehicle and helps them with any random checks that that may arise as part of our business operating procedures.
Immediate Fault Reporting on the road
Our new technology also enables the driver to report a fault with the vehicle, for example a faulty bulb, which can then be reported instantly to the depot, where an electronic notification is then sent to our workshop so that the correct part can be located and ordered. If there is a flat tyre, then a few button-presses on the tablet and a 3rd party will be on their way with a correct tyre replacement. There is also the ability to make calls on the tablets as a back-up to enable more complex discussions when required.
Any forms that need to be completed can now be done through simple menu choices and drop-down boxes rather than the need for paper. Importantly, some drivers who were less keen on writing or weren’t so good at it, have found the new tablets much better to use, and there are less errors and miscommunication with spelling.
By the time the driver gets back to the depot at the end of his shift the vehicle can then be taken straight into the workshop for repair. So, by the time the vehicle is next required, it's been fixed, and its ready to go. These changes significantly reduced the need for paper records between the office and the workshop. Additionally, the paperless project has delivered a critical benefit by reducing down time in the workshop and helped to keep our vehicles on the road collecting customer waste.
Cost Savings
The combination of carrying out pre-start checks and the live fault reporting has driven down the number of issues reported on the trucks, leading to more cost savings, from lower repair bills to less down time, with the trucks remaining on the road for longer.
In addition to these more obvious cost savings there have been some others.
For example, by analysing some of the reports available we have identified that we have had a regular occurrence of breaking a wing mirror on a Wednesday! By tracing this unique issue back through the vehicles' route we established that one particular customer location was proving difficult for our drivers to reach. By placing the bins in a different location or changing the truck that visits the customer we can avoid the situation arising again.
We’ve also managed to reduce the size of the vehicle hand books in the can from 50 pages to 20, further reducing the volume of paper we use.
Saving management time
By providing wider access to the data, reporting has become easier and decision making has been improved by enabling everyone to have access to the same information. And finding the right file has become much easier too!
Accepting change
There are always challenges with any business change programme and this project was no different. Although our drivers have had technology in the cab for some time there was a certain level of reassurance that paper provided. However, by using the new process our drivers have now become more confident with the technology and we are now beginning to see the benefits.
Lessons learnt
When asked about what learnings could be taken from this project, Neil said “In taking on a project like this I definitely underestimated the time it would take." However, Neil is delighted with the implementation and has a lot of personal satisfaction in finishing the project.
Neil is already enjoying the new management reporting information he has at his fingertips and can already see the hoped-for efficiencies coming good!
“I relied a lot on the talent of the people involved who definitely helped deliver the project.”
Neil Luce, Area Depot Manager, Hills Waste Solutions